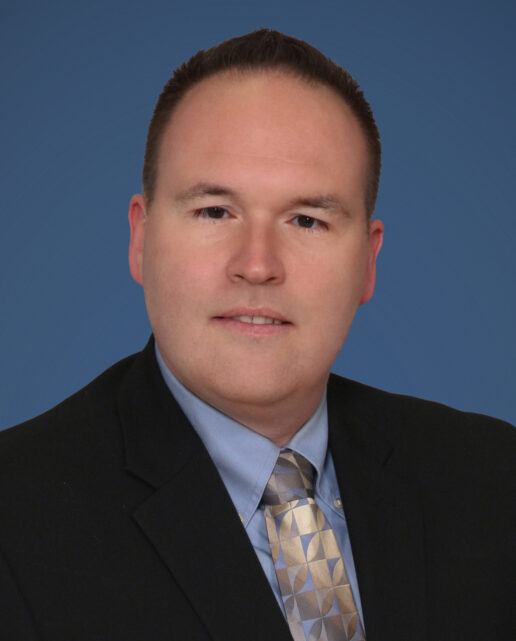
Ever had a customer return from camping and complain of a distinct odor of burnt electronics filling the air? The next thing that RVer knows, the water pump quits and the AC stops working. The consumer flips the switch for a circulating fan, but nothing happens. Even the stabilizer jacks will not operate.
If so, the culprit may be voltage variation from the incoming power source, which sometimes is hundreds of feet from the distribution transformer that supplies the varying demands of all the RVs connected to it. While that prime campsite might be perfect for the user, voltage variation can be hazardous for the RV’s electrical devices—especially its electric motors.
The National Electrical Manufacturers Association (NEMA) publishes industry standards for electric motors and generators that include specifications for voltage variation. According to its MG 1 standard, AC motors “shall operate successfully” at the rated load if the power source is within these parameters:
- Plus/minus 10 percent of rated voltage with rated frequency for induction motors.
- Plus/minus 6 percent of rated voltage with rated frequency for universal motors.
- 10 percent combined variation in rated voltage and frequency (sum of absolute values) if:
-
- Frequency is within plus/minus 5 percent of rated frequency.
- Voltage variation of universal motors (except fan motors) is within plus/minus 6 percent of rated voltage.
-
Frequency variation usually is not a problem in North America, where most RV electrical devices require 60 Hz rather than 50 Hz power. The allowable voltage variation is 6 to 10 percent, depending on the types of electric motors in the RV. These typically consist of AC induction, universal, DC and servo motors, as well as AC generators (alternators). The table below shows the voltage limits for 120 VAC and 230 VAC services for AC induction and universal motors.
Measuring the actual voltage at an RV hookup requires a digital multimeter (DMM). Consumer-grade DMMs are available from many reputable manufacturers, as is the required personal protective equipment (PPE). If in doubt, the user should ask maintenance personnel at the campsite to measure the hookup’s voltage.
Voltage Calculation Examples
Let’s suppose an RV has some universal motors, and the campground’s 230 VAC electrical service measures 215 VAC at the hookup. Table 1 shows the minimum acceptable voltage is 216.2 VAC, which means the supplied voltage is too low at that hookup.
Now assume the RV does not have any universal motors, and the 120 VAC service measures 127 VAC at the hookup. According to Table 1, the allowable limit at +10 percent is 132 VAC, making this service acceptable.
High/Low Voltage Effects on Motor Performance and Reliability
So, does operating within NEMA’s parameters influence electric motor performance and reliability? The short answer is yes. Even though the NEMA Std. MG 1 standard says various motor designs will operate within 6 to 10 percent of rated voltage, that limit does not accurately reflect what happens when motors run on high or low voltage. Any change from the rated voltage and frequency will affect the motor’s performance, sometimes dramatically.
The various electric motors in an RV may have different application-dependent magnetic flux characteristics, but the same principles still apply. For example, higher input voltage equals a higher magnetic flux. At some point, that will begin to saturate the motor’s core, causing it to heat up quickly and potentially damaging the motor’s insulation system.
A low voltage supply is more harmful than high voltage because it decreases the magnetic flux in the core iron. Not using the core iron optimally causes efficiency and torque to fall as the motor’s internal temperature begins to rise. In this scenario, motors tend to become overloaded doing the same work as before and often fail prematurely. Table 1 shows the typical effects of voltage variation on AC induction motors.
The following summary explains how over and under voltage typically affects induction motor performance.
• Torque. The torque of an induction motor varies as the square of the voltage, so any small variation in voltage will significantly affect the starting and maximum torque. At 110 percent voltage, torque will increase by 21 percent, but at 90 percent voltage, torque will decrease by 19 percent. This variation could pose a problem if the motor needs to start a high-inertia load.
• Speed. The speed will change slightly with high or low voltage, increasing about 1 percent at 110 percent voltage and decreasing about 1.5 percent at 90 percent voltage. But when you look at the speed change in percent slip, the numbers are more dramatic. Slip is the difference between the speed of the motor’s rotating magnetic field (synchronous speed) and how fast its shaft is turning. At 110 percent voltage, slip will decrease 17 percent; at 90 percent voltage, it will increase 23 percent.
• Energy efficiency. At 110 percent voltage, a motor may be up to 1 percent more efficient than at its rated voltage. At 90 percent voltage, however, a motor is about 2 percent less efficient. This difference in efficiency is especially important for larger motors, potentially increasing operating costs significantly.
• Current. At 110 percent voltage, the starting current will increase 10 to 12 percent, but the full-load current will decrease 7 percent. This may cause a problem if the power supply cannot handle the higher starting current. At 90 percent voltage, the starting current will decrease 10 to 12 percent, while the full-load current will increase 11 percent.
• Temperature rise. Variations in voltage also affect the temperature rise at full load. At 110 percent voltage, the temperature rise will decrease 3 to 4°C—unless the core has become magnetically saturated, causing the temperature to increase. At 90 percent voltage, the temperature rise will increase 6 to 7°C. Generally, every 10°C increase in total temperature rise reduces the insulation life by half. Even slight under-voltage will increase the temperature rise, shortening the life of the motor.
• Overload capacity. At 110 percent voltage, a motor will have a 21 percent higher overload capacity; at 90 percent voltage, that capacity will decrease by 19 percent. Motors often run overloaded for some period, so operating on under-voltage increases the possibility of premature failure.
Checking Service Voltage Is Critical
To ensure the reliability of an RV’s electrical devices, especially electric motors, campers must know the service voltage of the hookup their RV is using. Teaching consumers to check that before they plug in the vehicle could save them many headaches.
Although NEMA Std. MG 1 allows up to plus/minus 10 percent voltage variation for certain electric motors, performance and reliability may suffer if the service voltage is lower than the motor’s nameplate rating. Once your customers find that perfect RV campsite, have them check the voltage at the service box with a DMM and PPE before plugging in. This is a great opportunity to sell those devices in your retail store as well.
About the author
Matthew Conville, P.E. is a technical support specialist at EASA, Inc., St. Louis, Missouri. He can be reached at 314-993-2220. EASA is an international trade association of more than 1,800 firms in an estimated 70 countries that sell and service electromechanical apparatus. Learn more at www.easa.com.
120 VAC service | 230 VAC service | ||
Nominal | 120.0 VAC | Nominal | 230.0 VAC |
-6% | 112.8 VAC | -6 percent | 216.2 VAC |
+6% | 127.2 VAC | +6 percent | 243.8 VAC |
-10% | 108.0 VAC | -10 percent | 207.0 VAC |
+10% | 132.0 VAC | +10 percent | 253.0 VAC |