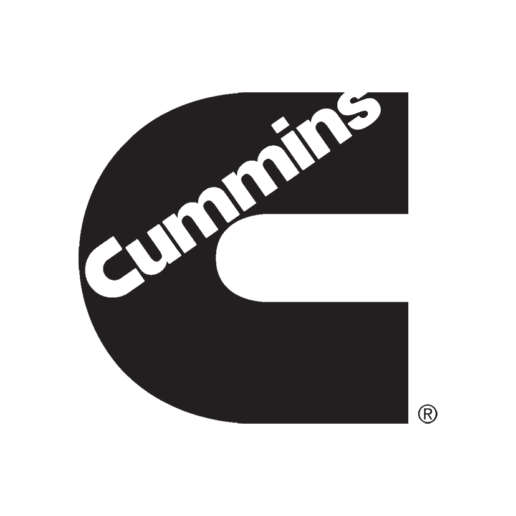
Cummins is temporarily closing four southern Indiana plants this week due to COVID-19-related disruptions. The news follows the Columbus, Indiana-based engine and generator manufacturer’s announcement of cuts to executive and employee pay.
The plant closures affect approximately 2,000 of Cummins 10,000 employees in Indiana. Employees at the shuttered plants will not be paid during the shutdown but will keep medical, dental and life insurance up to 90 days. A company spokesman said Cummins hopes to reopen the plants May 4, or sooner if there is demand.
Cummins’ warehouses in southern Indiana will stay open to support aftermarket operations, as will technical centers and parts distribution centers.
“The impact from the pandemic on the global economy has been sudden and is growing,” Cummins Chairman and CEO Tom Linebarger said, “and it is imperative for us to respond quickly to maintain our strong financial position.”
The company is reducing Linebarger’s salary 50 percent and cutting the board of directors’ compensation by 25 percent.
Cummins has more than 60,000 total employees in the United States and abroad. It is reducing salary for all U.S. employees between 10 and 25 percent and reducing working hours. The company is taking similar measures for employees based outside the U.S., depending on local regulations.
All reductions in pay are intended to be temporary, the company said. Cummins will re-evaluate pay at the end of the second quarter.
“These are difficult but necessary actions, and I know they will have a real impact on the lives of our employees and their families,” Linebarger said. “I appreciate their understanding and support as we work through these challenging times together. I want to thank our employees for their continued commitment to ensuring our customers receive the products and service they need to provide essential support to the global economy.”
Demand for engines is down, but Cummins has seen demand explode for components used to make N95 respirator masks. Cummins’ NanoNet and NanoForce technology, which uses DuPont’s Hybrid Membrane Technology (HMT), normally goes into the air, fuel and lube filtration products in the manufacturer’s heavy-duty diesel engines. However, the same technology also can be used in the N95 respirator masks worn by healthcare professionals to filter harmful airborne particles that can spread COVID-19. Cummins has donated the technology to make the masks.
The need for N95 masks has skyrocketed in recent weeks in response to the COVID-19 pandemic. Many of the world’s leading mask manufacturers are in need of the critical materials to assemble the mask and are struggling to meet demand.
“Cummins is re-evaluating our supply base and manufacturing capabilities to identify how we can support our healthcare professionals who rely on critical personal protective equipment to do their jobs,” Cummins Filtration Vice President Amy Davis said. “Our NanoNet Media can fill a key supply void and help address the mask shortage facing the United States and other countries around the world.”
The first mask prototypes using Cummins’ donated materials were assembled by University of Minnesota teams in March as part of an initiative to provide masks to M Health Fairview and other Minneapolis-based healthcare systems. As the COVID-19 outbreak escalated, the University of Minnesota realized its supply of N95 masks to protect healthcare workers would potentially run out in a matter of weeks. To address this challenge, a team of designers, engineers, chemists, surgeons, anesthesiologist and apparel and clothing experts from the University of Minnesota’s Institute for Engineering in Medicine; Medical School; College of Design; College of Science and Engineering; and Center for Filtration Research Consortium (CFR) came together to address this projected shortage of critical personal protective equipment.
“The first thing we recognized from our experts in the Center for Filtration Research, who work directly with Cummins, is that not all filtration materials are created equal, and that the Cummins material is an excellent alternative,” said Jakub Tolar, Medical School Dean at the University of Minnesota. “We are tremendously grateful for the generous donation from Cummins of their filtration materials toward our mask effort. Since the arrival of the filtration media, we have been able to make rapid progress, and we now believe we have several viable mask options, including both a disposable and reusable option. These designs show real promise in keeping our healthcare workers safe should standard medical supplies of N95 masks no longer be available.”