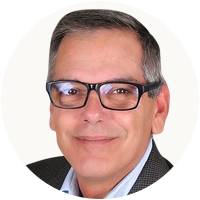
Typically, when analyzing dealership service data throughout the RV industry, we look at average repair event cycle times (RECT) for all work orders and their two main bottlenecks: work orders with warranty coverage and work orders with at least one out-of-stock part.
Over the past five years, 2022 has had the highest average RECT—averaging 38 days through September’s end. Work orders with warranty coverage averaged 55 days, while the average RECT for work orders with out-of-stock parts increased to 85 days.
For comparison, the base RECT, which includes work orders with no warranty coverage and all parts in stock, averaged just 17 days.
When doing the math, we find that warranty coverage is adding 38 days to the base cycle times and out-of-stock parts are adding 58 days. At a glance, out-of-stock parts seem the bigger issue.
A Little Closer Look
So far this year, the average cycle time for all work orders with warranty coverage has been 55 days. By looking at the actual impact of both bottlenecks combined, though, we see a different story.
Work orders with warranty coverage and all parts in stock, just one bottleneck, averaged 37-day cycle times. Work orders with warranty coverage and at least one out-of-stock part, both bottlenecks, averaged 104 days.
Warranty appears to be adding only a 20-day delay to the base cycle time, while out-of-stock parts are adding 87 days. That is a huge difference.
From this comparison alone, we can easily blame out-of-stock parts for all the delays. Right?
Not so fast.
Cycle times for all work orders with at least one out-of-stock part have averaged 85 days so far this year. Yes, that is huge.
However, when we review work orders with just one bottleneck, out-of-stock parts and no warranty coverage, cycle times are actually averaging 27 days this year.
Out-of-stock parts, on their own, are adding just 10-day delays to the average base cycle times. In 2018 and 2019, out-of-stock parts increased delays by four days on average. We are seeing an increase in the delays due to out-of-stock parts, but not substantially.
Why Does Out of Stock Get a Bad Rap?
Last year, we started tracking the impact of the two RECT bottlenecks combined. Peeling back the layers of data, we found a small percentage of work orders comprise a large portion of excessive RECT, especially the out-of-stock parts bottleneck.
Let me explain. To do so, we will need to talk about fractions.
Work orders with both warranty and out-of-stock bottlenecks make up a larger percentage of the out-of-stock parts bottleneck when compared with the warranty coverage bottleneck.
On average, 43% of all work orders had warranty coverage. Less than a quarter of those work orders had out-of-stock parts.
However, out-of-stock parts comprised about 22% of all work orders, with more than half of those work orders also having warranty coverage. So, these work orders had a greater impact because they make up such a large portion of the out-of-stock parts bottleneck.
Based on this graphic, you can see 47% of the work orders had no warranty and no out-of-stock parts. So, almost half of the customers had cycle times averaging 17 days.
About a third of consumers (31%) had work orders with warranty coverage and no out-of-stock parts. Those consumers had cycle times averaging 37 days.
Just 10% of all work orders had no warranty coverage and at least one out-of-stock part, and those customer cycle times averaged 27 days.
The resulting 12% of work orders had the double whammy, both warranty coverage and out-of-stock parts. Those average cycle times exceed 100 days. Although the group may represent just 12% of total work orders, they comprise 35% of the total RECT days.
Then Where Is the Real Delay?
To really dissect RECT, we break down each bottleneck into three major components.
For the warranty coverage bottleneck, we look at:
- Start Days—The number of days to start all the repairs;
- Job Days—The number of days to complete the repairs; and
- Delivery Days—The number of days to return the unit to the customer after the last repair.
For the out-of-stock parts bottleneck, we examine:
- ID Days—The number of days taken to identify (and order) all the parts needed;
- Lead Time Days—The number of days to receive all the parts; and
- Repair Wait Days—The number of days to complete the repairs after receiving the parts.
Start days, job days and repair wait days combined create both bottlenecks’ largest impact.
Warranty Start Days doubled the past two years. In 2018 and 2019, the average was 21 days. This year, that metric jumped to 42 days when a part had to be ordered. When there are no out-of-stock parts, however, start days average 15 days.
Warranty Job Days saw a similar increase when a part is out of stock. Job days, which averaged 21 days in 2018 and 2019, rose to a 37-day average this year. When all parts are in stock, though, job days averaged seven days when parts were in stock.
Out-Of-Stock Repair Wait Days also doubled when an RV had warranty coverage. Over the last two years, repair wait days jumped from a 17-day average in 2018 and 2019 to 33 days this year. Without warranty coverage, repair wait days averaged just 15 days.
By focusing on these specific components, you can better determine how both warranty coverage and out-of-stock parts are impacting your RECT.
By tracking these key indicators, you will be better positioned to improve your repair event cycle times and ultimately your customers’ satisfaction.
As you track your efforts over time, you can more easily see if your efforts were successful.
Your data is like gold; mine it often.
Don Miller is a senior data consultant at Constellation Dealer Group. With more than 30 years of experience in the industry, Miller provides training, consulting and analytical services to dealerships. He specializes in data analysis and worked extensively to educate dealerships on adopting a data-driven decision model. Miller created the IDS RECT report, an RVDA Chairman’s Service Award-winning report. The report is used globally by dealerships to deliver better customer experiences.